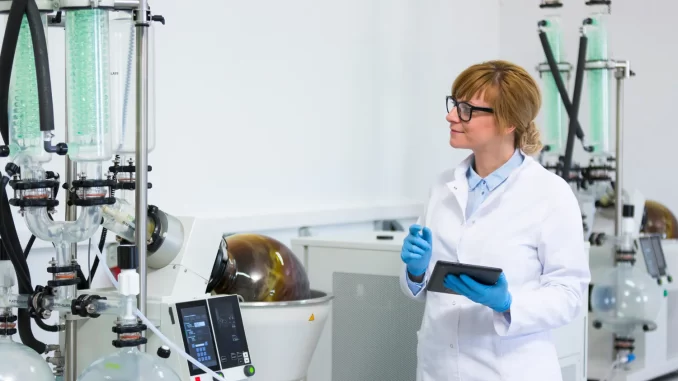
Destylacja rozpuszczalników to proces, który polega na oddzieleniu substancji na podstawie różnicy ich temperatur wrzenia. Jest to technika szeroko stosowana w chemii, przemyśle farmaceutycznym oraz w produkcji napojów alkoholowych. Proces ten zaczyna się od podgrzania mieszaniny, co powoduje parowanie substancji o najniższej temperaturze wrzenia. Para ta następnie przechodzi przez skraplacz, gdzie ulega schłodzeniu i kondensacji, tworząc ciecz, która jest zbierana jako destylat. W przypadku rozpuszczalników, destylacja pozwala na uzyskanie czystego związku chemicznego poprzez eliminację zanieczyszczeń lub innych składników o wyższej temperaturze wrzenia. Istnieją różne metody destylacji, takie jak destylacja prosta, frakcyjna czy też destylacja pod ciśnieniem atmosferycznym. Wybór odpowiedniej metody zależy od specyfiki rozpuszczalników oraz pożądanej czystości końcowego produktu.
Jakie są zastosowania destylacji rozpuszczalników w przemyśle
Destylacja rozpuszczalników znajduje szerokie zastosowanie w różnych gałęziach przemysłu, co czyni ją kluczowym procesem technologicznym. W przemyśle chemicznym jest wykorzystywana do oczyszczania surowców oraz produkcji wysokopurejnych substancji chemicznych. Na przykład, w produkcji alkoholi etylowych, destylacja pozwala na oddzielenie etanolu od wody i innych związków, co jest niezbędne do uzyskania napojów wysokoprocentowych. W przemyśle farmaceutycznym proces ten jest stosowany do izolacji aktywnych składników leków oraz ich oczyszczania z zanieczyszczeń. Ponadto, destylacja rozpuszczalników jest również wykorzystywana w przemyśle petrochemicznym do separacji różnych frakcji ropy naftowej, takich jak benzyna czy olej napędowy. Dzięki tym zastosowaniom możliwe jest uzyskanie produktów o wysokiej czystości i jakości, które są niezbędne do dalszej obróbki oraz wykorzystania w różnych procesach technologicznych.
Jakie są różne metody destylacji rozpuszczalników
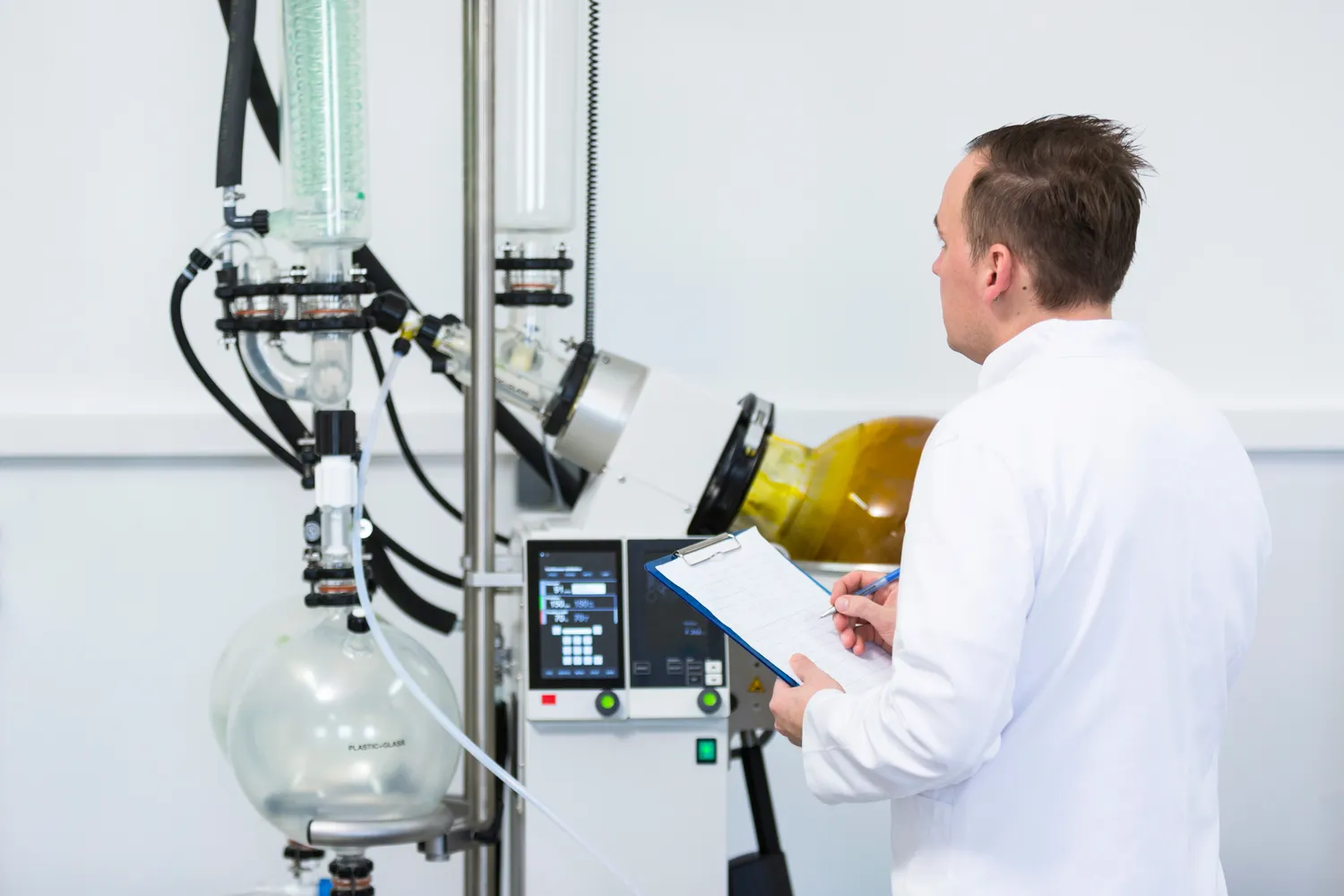
W kontekście destylacji rozpuszczalników istnieje kilka metod, które różnią się między sobą zarówno zasadą działania, jak i zastosowaniem. Najpopularniejszą z nich jest destylacja prosta, która polega na podgrzewaniu cieczy i zbieraniu pary o najniższej temperaturze wrzenia. Jest to metoda stosunkowo łatwa i tania, jednak jej skuteczność maleje w przypadku mieszanin o zbliżonych temperaturach wrzenia. Z tego powodu w takich przypadkach stosuje się destylację frakcyjną, która wykorzystuje kolumny frakcyjne do lepszego oddzielania poszczególnych składników mieszanki. Ta metoda pozwala na uzyskanie wyższej czystości produktów końcowych i jest powszechnie stosowana w przemyśle chemicznym oraz petrochemicznym. Inną metodą jest destylacja pod ciśnieniem atmosferycznym lub próżniowym, która umożliwia przeprowadzanie procesu w niższych temperaturach, co jest korzystne dla substancji termolabilnych.
Jakie są korzyści płynące z używania destylacji rozpuszczalników
Korzyści płynące z używania destylacji rozpuszczalników są liczne i mają istotny wpływ na jakość produktów oraz efektywność procesów przemysłowych. Przede wszystkim, dzięki temu procesowi możliwe jest uzyskanie wysokiej czystości substancji chemicznych, co jest kluczowe w wielu branżach, takich jak farmaceutyka czy chemia przemysłowa. Czyste rozpuszczalniki są niezbędne do prowadzenia reakcji chemicznych oraz produkcji leków o określonych właściwościach terapeutycznych. Ponadto, destylacja pozwala na efektywne usuwanie zanieczyszczeń i niepożądanych składników z mieszanin chemicznych, co przekłada się na poprawę jakości finalnych produktów. Kolejną korzyścią jest możliwość recyklingu rozpuszczalników, co przyczynia się do zmniejszenia kosztów produkcji oraz ochrony środowiska poprzez ograniczenie ilości odpadów chemicznych. Dodatkowo rozwój technologii związanych z destylacją przyczynia się do zwiększenia efektywności energetycznej procesów przemysłowych oraz obniżenia emisji szkodliwych substancji do atmosfery.
Jakie są wyzwania związane z destylacją rozpuszczalników
Destylacja rozpuszczalników, mimo licznych korzyści, wiąże się również z pewnymi wyzwaniami, które mogą wpływać na efektywność procesu oraz jakość uzyskiwanych produktów. Jednym z głównych problemów jest konieczność precyzyjnego doboru parametrów procesu, takich jak temperatura i ciśnienie, co wymaga zaawansowanej wiedzy technicznej oraz doświadczenia. Niewłaściwe ustawienia mogą prowadzić do niepełnej separacji składników, co skutkuje obniżoną czystością destylatu. Kolejnym wyzwaniem jest zarządzanie dużymi ilościami energii potrzebnej do przeprowadzenia procesu destylacji, co może generować znaczące koszty operacyjne. W przypadku dużych instalacji przemysłowych, optymalizacja zużycia energii staje się kluczowym zagadnieniem. Dodatkowo, niektóre substancje chemiczne mogą być toksyczne lub łatwopalne, co stawia przed operatorami dodatkowe wymagania dotyczące bezpieczeństwa pracy oraz ochrony środowiska. W związku z tym konieczne jest wdrażanie odpowiednich procedur bezpieczeństwa oraz systemów monitorowania, aby minimalizować ryzyko wypadków i emisji szkodliwych substancji.
Jakie są innowacje w technologii destylacji rozpuszczalników
W ostatnich latach obserwuje się dynamiczny rozwój innowacji w technologii destylacji rozpuszczalników, które mają na celu poprawę efektywności procesów oraz zwiększenie ich ekologiczności. Jednym z kierunków rozwoju jest zastosowanie nowoczesnych materiałów konstrukcyjnych w budowie kolumn destylacyjnych, co pozwala na lepsze przewodnictwo cieplne oraz zwiększenie powierzchni kontaktu między fazami gazową a ciekłą. Dzięki temu możliwe jest osiągnięcie wyższej wydajności separacji przy mniejszych stratach energii. Kolejnym trendem jest automatyzacja procesów destylacyjnych, która umożliwia dokładniejsze monitorowanie i kontrolowanie parametrów pracy instalacji. Systemy oparte na sztucznej inteligencji mogą analizować dane w czasie rzeczywistym i dostosowywać ustawienia w celu optymalizacji procesu. Innowacje obejmują również rozwój technologii membranowych, które mogą stanowić alternatywę dla tradycyjnej destylacji w niektórych zastosowaniach. Membrany selektywnie przepuszczające określone składniki mieszanki mogą znacznie zmniejszyć zużycie energii i czasu potrzebnego na separację.
Jakie są różnice między destylacją a innymi metodami separacji
Destylacja rozpuszczalników to jedna z wielu metod separacji składników mieszanin chemicznych, ale różni się od innych technik pod względem zasad działania oraz zastosowań. Na przykład, ekstrakcja to metoda polegająca na wykorzystaniu rozpuszczalnika do wydobycia pożądanych składników z mieszaniny. W przeciwieństwie do destylacji, która opiera się na różnicy temperatur wrzenia, ekstrakcja bazuje na różnicach w rozpuszczalności substancji w różnych cieczy. Ta metoda jest często stosowana w przemyśle spożywczym oraz farmaceutycznym do izolacji naturalnych związków chemicznych. Inną popularną metodą jest chromatografia, która wykorzystuje różnice w adsorpcji składników na stałym nośniku do ich separacji. Chromatografia jest niezwykle precyzyjna i pozwala na uzyskanie bardzo czystych frakcji, jednak jej zastosowanie może być ograniczone przez wysokie koszty sprzętu oraz czasochłonność procesu. Z kolei filtracja to metoda mechaniczna polegająca na oddzieleniu ciał stałych od cieczy lub gazu za pomocą porowatego materiału. Choć filtracja jest prostsza i tańsza niż destylacja, nie nadaje się do separacji składników o podobnych właściwościach fizykochemicznych.
Jakie są przyszłe kierunki badań nad destylacją rozpuszczalników
Przyszłość badań nad destylacją rozpuszczalników zapowiada się obiecująco dzięki rosnącemu zainteresowaniu zrównoważonym rozwojem oraz efektywnością energetyczną procesów przemysłowych. Jednym z kluczowych kierunków badań jest rozwój nowych materiałów do budowy kolumn destylacyjnych, które mogłyby poprawić wydajność separacji przy jednoczesnym zmniejszeniu zużycia energii. Badania nad nanomateriałami oraz ich zastosowaniem w procesach separacyjnych mogą przynieść rewolucyjne zmiany w tej dziedzinie. Ponadto naukowcy koncentrują się na opracowywaniu bardziej ekologicznych rozpuszczalników oraz metod ich regeneracji, co ma na celu ograniczenie negatywnego wpływu na środowisko naturalne. Innowacje w zakresie automatyzacji i cyfryzacji procesów destylacyjnych również będą miały istotny wpływ na przyszłość tej technologii. Wykorzystanie sztucznej inteligencji do analizy danych procesowych może przyczynić się do optymalizacji pracy instalacji oraz zwiększenia bezpieczeństwa operacyjnego. Również badania nad integracją różnych metod separacyjnych mogą prowadzić do stworzenia bardziej efektywnych systemów produkcyjnych, które łączą zalety różnych technik w jednym procesie.
Jakie są aspekty ekologiczne związane z destylacją rozpuszczalników
Aspekty ekologiczne związane z destylacją rozpuszczalników są coraz bardziej istotne w kontekście globalnych wyzwań związanych ze zmianami klimatycznymi oraz ochroną środowiska naturalnego. Proces ten wiąże się z zużyciem znacznych ilości energii, co generuje emisję gazów cieplarnianych oraz innych substancji szkodliwych dla atmosfery. Dlatego też wiele firm przemysłowych podejmuje działania mające na celu zwiększenie efektywności energetycznej swoich instalacji destylacyjnych poprzez modernizację sprzętu oraz wdrażanie innowacyjnych technologii. Ponadto ważnym aspektem ekologicznym jest zarządzanie odpadami powstającymi podczas procesu destylacji. Odpady te mogą zawierać toksyczne substancje chemiczne, dlatego ich odpowiednie składowanie i utylizacja są kluczowe dla ochrony środowiska. Coraz częściej stosuje się również metody recyklingu rozpuszczalników, co pozwala na ponowne wykorzystanie surowców i zmniejszenie ilości odpadów chemicznych generowanych przez przemysł. Warto również zwrócić uwagę na rozwój tzw. zielonej chemii, która promuje stosowanie bardziej ekologicznych reagentów oraz procesów produkcyjnych o mniejszym wpływie na środowisko.