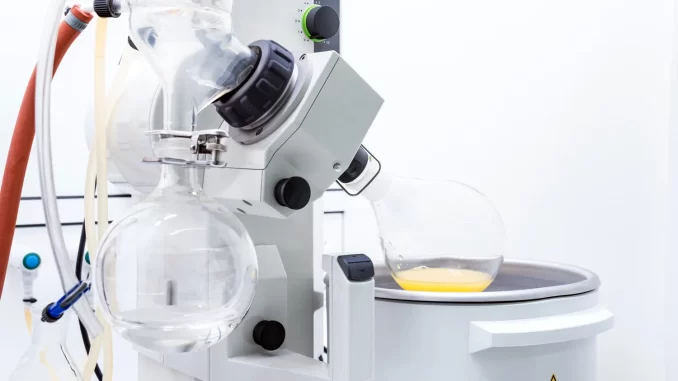
Destylarka do rozpuszczalników to urządzenie, które wykorzystuje proces destylacji do oddzielania różnych substancji chemicznych na podstawie ich temperatury wrzenia. W praktyce oznacza to, że gdy mieszanka rozpuszczalników jest podgrzewana, składniki o niższej temperaturze wrzenia parują jako pierwsze. Para ta jest następnie schładzana i kondensowana z powrotem w cieczy, co pozwala na zbieranie czystego rozpuszczalnika. Proces ten może być stosowany w różnych dziedzinach, od przemysłu chemicznego po laboratoria badawcze. Kluczowym elementem każdej destylarki jest kolumna destylacyjna, która zwiększa efektywność separacji dzięki wielokrotnemu skraplaniu i parowaniu. W zależności od konstrukcji destylarki, można uzyskać różne poziomy czystości końcowego produktu. Ważne jest również, aby pamiętać o bezpieczeństwie podczas pracy z takimi urządzeniami, ponieważ wiele rozpuszczalników jest łatwopalnych lub toksycznych.
Jakie są zastosowania destylarek do rozpuszczalników
Destylarki do rozpuszczalników znajdują szerokie zastosowanie w różnych branżach przemysłowych oraz w laboratoriach badawczych. W przemyśle chemicznym są wykorzystywane do oczyszczania surowców oraz produkcji wysokiej jakości chemikaliów. Dzięki procesowi destylacji można uzyskać czyste substancje, które są niezbędne w produkcji farb, lakierów czy tworzyw sztucznych. W laboratoriach badawczych destylarki służą do analizy składu chemicznego próbek oraz do przygotowywania roztworów o określonym stężeniu. Ponadto, destylarki są także wykorzystywane w przemyśle farmaceutycznym do produkcji leków oraz substancji czynnych. W ostatnich latach rośnie również zainteresowanie domowymi destylarkami, które pozwalają na produkcję własnych ekstraktów czy olejków eterycznych.
Jakie rodzaje destylarek do rozpuszczalników istnieją na rynku
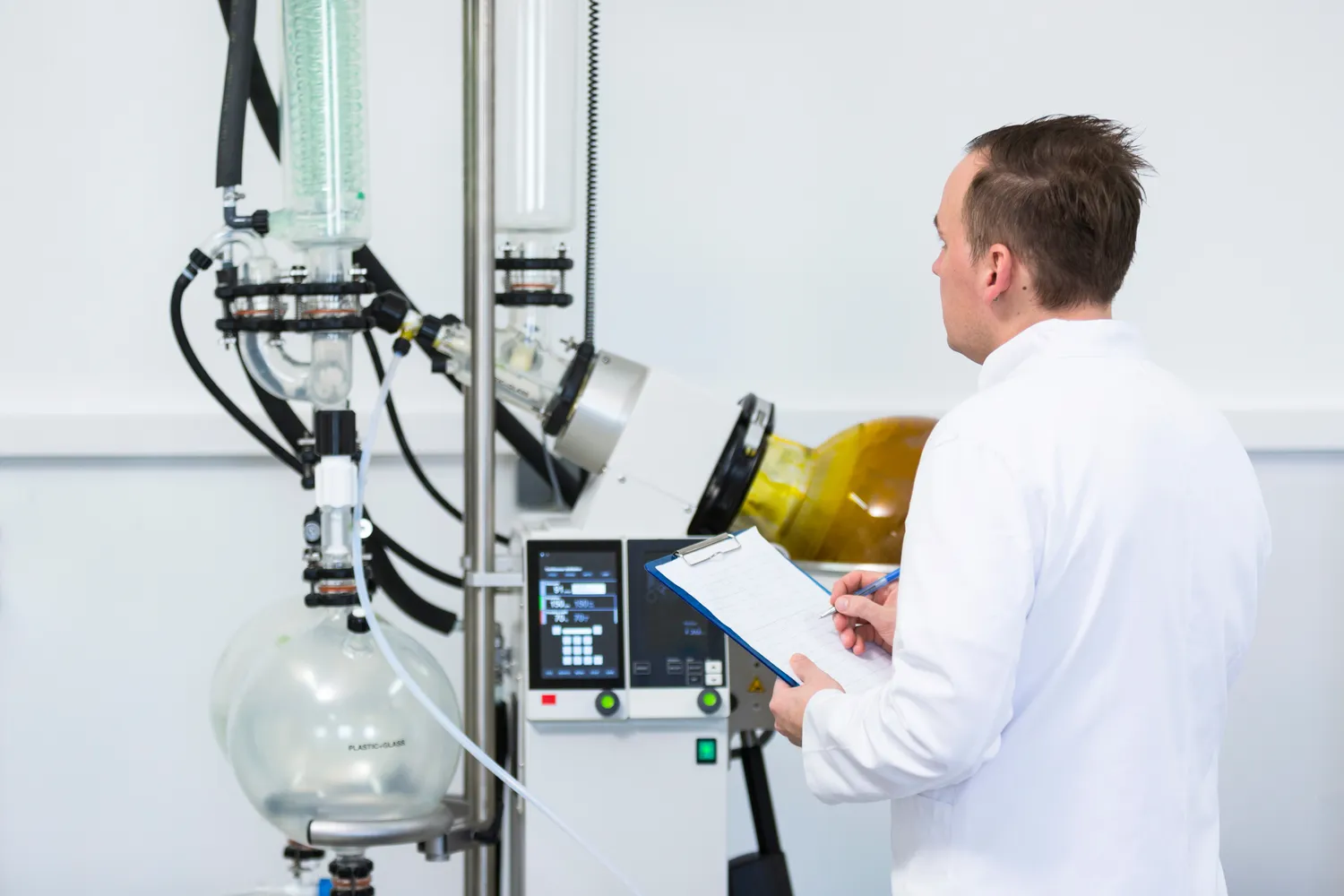
Na rynku dostępnych jest wiele rodzajów destylarek do rozpuszczalników, które różnią się konstrukcją oraz zastosowaniem. Jednym z najpopularniejszych typów są destylarki prostokątne, które charakteryzują się prostą budową i łatwością obsługi. Są one idealne dla osób początkujących lub dla tych, którzy potrzebują urządzenia do sporadycznego użytku. Innym rodzajem są destylarki kolumnowe, które oferują wyższą efektywność separacji dzięki zastosowaniu kolumny destylacyjnej. Te urządzenia są często wykorzystywane w przemyśle chemicznym oraz laboratoriach badawczych ze względu na swoją zdolność do produkcji bardzo czystych substancji. Istnieją także bardziej zaawansowane modele, takie jak destylarki próżniowe, które umożliwiają przeprowadzanie procesu destylacji w obniżonym ciśnieniu. Dzięki temu możliwe jest oddzielanie substancji o wysokiej temperaturze wrzenia bez ryzyka ich degradacji.
Jakie materiały są używane w budowie destylarek
Budowa destylarek do rozpuszczalników opiera się na różnych materiałach, które muszą spełniać określone wymagania dotyczące odporności chemicznej oraz termicznej. Najczęściej stosowanym materiałem jest stal nierdzewna, która charakteryzuje się wysoką odpornością na korozję oraz łatwością w utrzymaniu czystości. Stal nierdzewna zapewnia również długą żywotność urządzenia, co jest istotne w przypadku intensywnego użytkowania. Inne materiały używane w budowie to szkło borokrzemowe oraz teflon, które często stosowane są w elementach kontaktujących się z substancjami chemicznymi. Szkło borokrzemowe ma tę zaletę, że jest odporne na wysokie temperatury i działanie wielu chemikaliów, co czyni je idealnym materiałem dla laboratoriów. Teflon natomiast jest stosowany tam, gdzie wymagana jest dodatkowa odporność na przywieranie substancji oraz łatwość czyszczenia.
Jakie są koszty zakupu i eksploatacji destylarek
Koszty zakupu i eksploatacji destylarek do rozpuszczalników mogą się znacznie różnić w zależności od rodzaju urządzenia oraz jego przeznaczenia. Na rynku dostępne są zarówno proste modele dla amatorów, jak i zaawansowane urządzenia przemysłowe o dużej wydajności. Ceny podstawowych modeli zaczynają się od kilkuset złotych, natomiast profesjonalne destylarki mogą kosztować kilka tysięcy złotych lub więcej. Oprócz kosztu zakupu warto również uwzględnić wydatki związane z eksploatacją urządzenia. Do najważniejszych kosztów należy zaliczyć energię elektryczną potrzebną do podgrzewania mieszanki oraz ewentualne koszty konserwacji i naprawy sprzętu. Dodatkowo należy pamiętać o kosztach zakupu surowców chemicznych oraz ewentualnych materiałów eksploatacyjnych takich jak filtry czy uszczelki.
Jakie są najczęstsze problemy z destylarkami do rozpuszczalników
Podczas użytkowania destylarek do rozpuszczalników mogą wystąpić różne problemy, które mogą wpłynąć na efektywność procesu destylacji oraz jakość uzyskiwanego produktu. Jednym z najczęstszych problemów jest niewłaściwe ustawienie temperatury, co może prowadzić do niepełnej separacji składników. Zbyt niska temperatura może spowodować, że niektóre substancje nie odparują, podczas gdy zbyt wysoka może doprowadzić do ich degradacji. Kolejnym problemem jest zatykanie się kolumny destylacyjnej lub innych elementów urządzenia, co może być spowodowane osadzaniem się zanieczyszczeń lub resztek chemikaliów. Regularne czyszczenie i konserwacja sprzętu są kluczowe dla uniknięcia takich sytuacji. Inne trudności mogą wynikać z niewłaściwego podłączenia destylarki do źródła ciepła lub chłodzenia, co również wpływa na efektywność procesu. W przypadku bardziej zaawansowanych modeli mogą wystąpić problemy z elektroniką lub systemami automatyzacji, które wymagają specjalistycznej wiedzy do naprawy.
Jakie są zalety używania destylarek do rozpuszczalników w laboratoriach
Używanie destylarek do rozpuszczalników w laboratoriach przynosi wiele korzyści, które przyczyniają się do poprawy efektywności pracy oraz jakości uzyskiwanych wyników. Przede wszystkim, proces destylacji pozwala na uzyskanie wysokiej czystości substancji chemicznych, co jest kluczowe w badaniach naukowych oraz w produkcji farmaceutycznej. Dzięki temu można uniknąć kontaminacji próbek oraz zapewnić dokładność analiz chemicznych. Ponadto, destylarki umożliwiają recykling rozpuszczalników, co przyczynia się do zmniejszenia kosztów operacyjnych oraz ograniczenia negatywnego wpływu na środowisko. W laboratoriach często zachodzi potrzeba przygotowywania roztworów o określonym stężeniu, a destylacja pozwala na precyzyjne kontrolowanie tego procesu. Dodatkowo nowoczesne destylarki wyposażone są w systemy automatyzacji, które zwiększają komfort pracy oraz minimalizują ryzyko błędów ludzkich.
Jakie są różnice między destylacją prostą a frakcyjną
Destylacja prosta i frakcyjna to dwa podstawowe rodzaje procesów stosowanych w destylarkach do rozpuszczalników, które różnią się zarówno zasadą działania, jak i zastosowaniem. Destylacja prosta polega na jednorazowym podgrzewaniu mieszanki cieczy i zbieraniu pary o niższej temperaturze wrzenia. Jest to proces stosunkowo szybki i łatwy w wykonaniu, jednak jego skuteczność ogranicza się do separacji substancji o znacznie różniących się temperaturach wrzenia. Z kolei destylacja frakcyjna jest bardziej skomplikowanym procesem, który wykorzystuje kolumnę destylacyjną do wielokrotnego skraplania i parowania substancji. Dzięki temu możliwe jest oddzielanie składników o podobnych temperaturach wrzenia, co jest szczególnie istotne w przypadku mieszanin zawierających wiele różnych substancji chemicznych. Destylacja frakcyjna jest często stosowana w przemyśle chemicznym oraz w laboratoriach badawczych ze względu na swoją wysoką efektywność i zdolność do produkcji bardzo czystych substancji.
Jakie są kluczowe czynniki wpływające na wydajność destylacji
Wydajność procesu destylacji w dużej mierze zależy od kilku kluczowych czynników, które należy uwzględnić podczas projektowania i eksploatacji destylarki do rozpuszczalników. Pierwszym z nich jest temperatura podgrzewania mieszanki cieczy, która powinna być dostosowana do charakterystyki składników chemicznych. Zbyt niska temperatura może prowadzić do niepełnej separacji substancji, natomiast zbyt wysoka może powodować ich degradację. Kolejnym istotnym czynnikiem jest ciśnienie atmosferyczne; obniżone ciśnienie sprzyja odparowywaniu substancji o wysokiej temperaturze wrzenia bez ryzyka ich uszkodzenia. Ważna jest także konstrukcja kolumny destylacyjnej oraz jej długość; im dłuższa kolumna, tym większa szansa na skuteczną separację składników dzięki wielokrotnemu skraplaniu i parowaniu. Również prędkość przepływu pary ma znaczenie; zbyt szybki przepływ może prowadzić do nieefektywnej separacji, podczas gdy zbyt wolny może powodować straty ciepła i obniżać wydajność całego procesu.
Jakie są przepisy prawne dotyczące użytkowania destylarek
Użytkowanie destylarek do rozpuszczalników wiąże się z przestrzeganiem określonych przepisów prawnych oraz norm bezpieczeństwa, które mają na celu ochronę zdrowia ludzi oraz środowiska naturalnego. W wielu krajach istnieją regulacje dotyczące przechowywania i używania substancji chemicznych, które obejmują również zasady dotyczące użytkowania urządzeń takich jak destylarki. Użytkownicy muszą być świadomi wymagań dotyczących wentylacji pomieszczeń roboczych oraz stosowania odpowiednich środków ochrony osobistej podczas pracy z łatwopalnymi lub toksycznymi substancjami. W przypadku przemysłowego użycia destylarek konieczne może być uzyskanie odpowiednich zezwoleń oraz przeprowadzenie ocen ryzyka związanych z ich eksploatacją. Ponadto wiele krajów wymaga regularnych inspekcji sprzętu oraz przestrzegania norm dotyczących emisji substancji chemicznych do atmosfery czy wód gruntowych.
Jakie innowacje technologiczne wpływają na rozwój destylarek
W ostatnich latach obserwuje się dynamiczny rozwój technologii związanych z produkcją i użytkowaniem destylarek do rozpuszczalników, co przekłada się na ich efektywność oraz bezpieczeństwo użytkowania. Nowoczesne modele często wyposażone są w zaawansowane systemy automatyzacji, które umożliwiają precyzyjne kontrolowanie parametrów procesu destylacji takich jak temperatura czy ciśnienie. Dzięki zastosowaniu inteligentnych czujników możliwe jest monitorowanie stanu urządzenia w czasie rzeczywistym oraz automatyczne dostosowywanie ustawień w celu optymalizacji wydajności procesu. Innowacyjne materiały wykorzystywane w budowie destylarek również przyczyniają się do poprawy ich funkcjonalności; nowe kompozyty czy powłoki teflonowe zwiększają odporność na działanie agresywnych substancji chemicznych oraz ułatwiają czyszczenie urządzeń. Dodatkowo rozwój technologii ekologicznych sprawia, że coraz więcej producentów stawia na energooszczędne rozwiązania oraz recykling rozpuszczalników, co ma pozytywny wpływ na ochronę środowiska naturalnego.