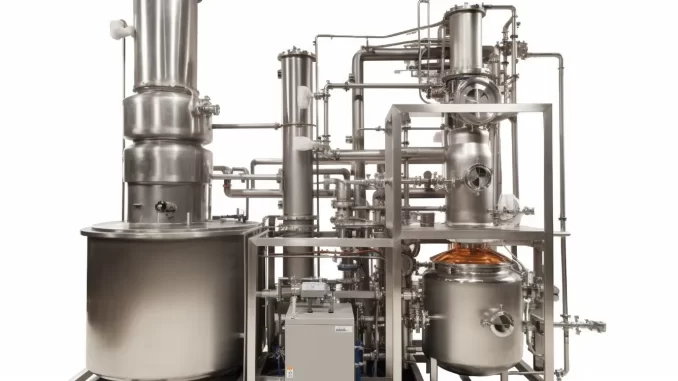
Destylarki do rozpuszczalników to urządzenia, które wykorzystują proces destylacji do oddzielania różnych substancji chemicznych na podstawie ich temperatury wrzenia. W praktyce oznacza to, że rozpuszczalniki są podgrzewane, a następnie ich opary są schładzane i kondensowane z powrotem w cieczy. Proces ten jest niezwykle efektywny, ponieważ pozwala na uzyskanie czystych substancji chemicznych, które mogą być używane w różnych aplikacjach przemysłowych i laboratoryjnych. W destylacji prostej, która jest najczęściej stosowaną metodą, jedna substancja jest oddzielana od drugiej na podstawie różnicy w temperaturze wrzenia. W przypadku bardziej skomplikowanych mieszanin chemicznych stosuje się destylację frakcyjną, która umożliwia oddzielenie kilku składników jednocześnie. Dzięki zastosowaniu kolumn frakcyjnych możliwe jest uzyskanie wyższej czystości produktów końcowych.
Jakie rodzaje destylarek do rozpuszczalników są dostępne
Na rynku dostępne są różne rodzaje destylarek do rozpuszczalników, które różnią się zarówno konstrukcją, jak i przeznaczeniem. Najpopularniejsze z nich to destylarki laboratoryjne, które są zaprojektowane do pracy w warunkach kontrolowanych i umożliwiają precyzyjne oddzielanie substancji chemicznych. W laboratoriach często stosuje się destylarki prostokątne oraz okrągłe, które różnią się kształtem naczynia destylacyjnego. Oprócz tego istnieją również destylarki przemysłowe, które są znacznie większe i przeznaczone do ciągłej produkcji dużych ilości rozpuszczalników. Te urządzenia często wyposażone są w zaawansowane systemy automatyzacji, co pozwala na monitorowanie i kontrolowanie procesu destylacji w czasie rzeczywistym. Istnieją także destylarki mobilne, które można łatwo przemieszczać i wykorzystywać w różnych lokalizacjach.
Jakie zastosowania mają destylarki do rozpuszczalników
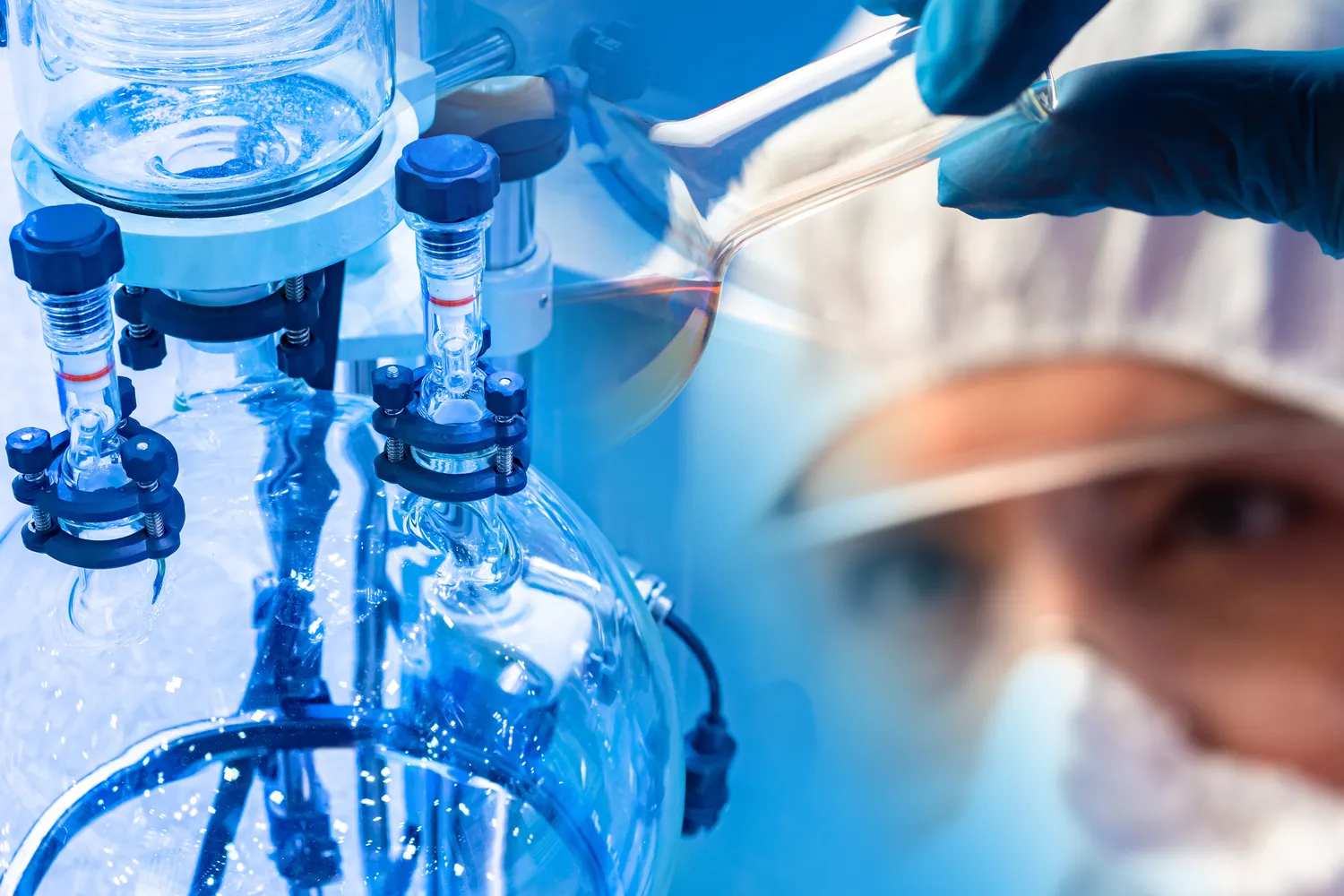
Destylarki do rozpuszczalników mają szerokie zastosowanie w różnych dziedzinach przemysłu oraz nauki. W laboratoriach chemicznych służą głównie do oczyszczania substancji chemicznych oraz przygotowywania próbek do dalszych badań. Dzięki nim można uzyskać wysokiej czystości rozpuszczalniki, które są niezbędne w wielu eksperymentach. W przemyśle farmaceutycznym destylarki odgrywają kluczową rolę w produkcji leków oraz substancji czynnych, gdzie czystość składników jest niezwykle istotna dla skuteczności terapii. W branży petrochemicznej wykorzystuje się je do separacji różnych frakcji ropy naftowej oraz produkcji paliw. Destylarki znajdują również zastosowanie w przemyśle kosmetycznym, gdzie służą do pozyskiwania olejków eterycznych oraz innych składników aktywnych wykorzystywanych w kosmetykach.
Jakie są kluczowe aspekty wyboru destylarki do rozpuszczalników
Wybór odpowiedniej destylarki do rozpuszczalników jest kluczowy dla efektywności procesu destylacji oraz jakości uzyskiwanych produktów. Przede wszystkim należy zwrócić uwagę na pojemność urządzenia, która powinna być dostosowana do potrzeb użytkownika oraz skali produkcji. Ważnym aspektem jest także rodzaj materiałów użytych do budowy destylarki, ponieważ muszą one być odporne na działanie chemikaliów oraz wysokich temperatur. Kolejnym istotnym czynnikiem jest wydajność energetyczna urządzenia – nowoczesne modele często wyposażone są w technologie oszczędzające energię, co może znacząco obniżyć koszty eksploatacji. Należy również zwrócić uwagę na systemy bezpieczeństwa oraz automatyzacji procesów, które mogą ułatwić obsługę urządzenia i zwiększyć jego niezawodność. Warto także zastanowić się nad serwisem posprzedażowym oraz dostępnością części zamiennych, co ma znaczenie dla długoterminowej eksploatacji sprzętu.
Jakie są najczęstsze problemy z destylarkami do rozpuszczalników
Podczas użytkowania destylarek do rozpuszczalników mogą wystąpić różne problemy, które mogą wpływać na efektywność procesu destylacji oraz jakość uzyskiwanych produktów. Jednym z najczęstszych problemów jest zatykanie kolumny frakcyjnej, co może prowadzić do obniżenia wydajności destylacji. Zatykanie to często spowodowane jest osadami chemicznymi, które gromadzą się w trakcie procesu. Aby temu zapobiec, ważne jest regularne czyszczenie urządzenia oraz stosowanie odpowiednich filtrów. Innym problemem może być niewłaściwe ustawienie temperatury, co może prowadzić do niepełnej separacji składników. Użytkownicy powinni dokładnie monitorować temperaturę wrzenia substancji oraz dostosowywać parametry pracy destylarki w zależności od rodzaju przetwarzanych rozpuszczalników. Dodatkowo, awarie systemów chłodzenia mogą prowadzić do nieefektywnego kondensowania oparów, co również wpływa na jakość końcowego produktu. Warto również zwrócić uwagę na uszczelki i połączenia, które mogą ulegać zużyciu i prowadzić do wycieków substancji chemicznych.
Jakie są zalety korzystania z nowoczesnych destylarek do rozpuszczalników
Nowoczesne destylarki do rozpuszczalników oferują szereg zalet, które znacząco poprawiają efektywność procesów przemysłowych i laboratoryjnych. Przede wszystkim, wiele z nich jest wyposażonych w zaawansowane systemy automatyzacji, które umożliwiają precyzyjne kontrolowanie parametrów pracy, takich jak temperatura czy ciśnienie. Dzięki temu możliwe jest uzyskanie wyższej czystości produktów oraz zwiększenie wydajności procesu destylacji. Nowoczesne modele często charakteryzują się także lepszą izolacją termiczną, co przekłada się na mniejsze straty energii i niższe koszty eksploatacji. Dodatkowo, innowacyjne technologie stosowane w produkcji destylarek pozwalają na łatwiejsze czyszczenie i konserwację urządzeń, co zwiększa ich żywotność i niezawodność. Wiele nowoczesnych destylarek jest również zaprojektowanych z myślą o bezpieczeństwie użytkowników, wyposażonych w systemy alarmowe oraz zabezpieczenia przed przegrzaniem czy wyciekiem substancji chemicznych.
Jakie są różnice między destylacją prostą a frakcyjną
Destylacja prosta i frakcyjna to dwa podstawowe rodzaje procesów destylacyjnych, które różnią się zarówno zastosowaniem, jak i techniką wykonania. Destylacja prosta jest najłatwiejszą formą tego procesu i polega na podgrzewaniu cieczy do momentu jej wrzenia, a następnie skraplaniu oparów w celu uzyskania czystego składnika. Jest to metoda skuteczna w przypadku mieszanin zawierających substancje o znacznie różnych temperaturach wrzenia. Z kolei destylacja frakcyjna jest bardziej skomplikowanym procesem, który wykorzystuje kolumny frakcyjne do oddzielania kilku składników jednocześnie. W tej metodzie opary przechodzą przez kolumnę, gdzie wielokrotnie skraplają się i parują, co pozwala na stopniowe oddzielanie substancji na podstawie ich temperatur wrzenia. Destylacja frakcyjna jest szczególnie przydatna w przypadku mieszanin zawierających substancje o zbliżonych temperaturach wrzenia, ponieważ umożliwia uzyskanie wyższej czystości produktów końcowych.
Jakie są kluczowe elementy budowy destylarki do rozpuszczalników
Budowa destylarki do rozpuszczalników opiera się na kilku kluczowych elementach, które współpracują ze sobą w celu efektywnego przeprowadzenia procesu destylacji. Podstawowym elementem jest naczynie destylacyjne, w którym odbywa się podgrzewanie cieczy. Naczynie to powinno być wykonane z materiałów odpornych na działanie wysokich temperatur oraz chemikaliów. Kolejnym istotnym elementem jest system chłodzenia, który ma za zadanie kondensować opary powstające podczas podgrzewania cieczy. Chłodnica może mieć różne formy – od prostych chłodnic rurowych po bardziej skomplikowane systemy z wymiennikami ciepła. Ważnym komponentem jest także kolumna frakcyjna, która umożliwia separację składników w przypadku destylacji frakcyjnej. Kolumna ta zawiera różne elementy takie jak talerze czy packingi, które zwiększają powierzchnię kontaktu między oparami a cieczą skraplającą się. Dodatkowo nie można zapomnieć o systemach pomiarowych oraz kontrolnych, które monitorują parametry pracy urządzenia i zapewniają jego bezpieczne funkcjonowanie.
Jak dbać o bezpieczeństwo podczas pracy z destylarkami
Praca z destylarkami do rozpuszczalników wiąże się z pewnymi zagrożeniami, dlatego niezwykle ważne jest przestrzeganie zasad bezpieczeństwa podczas ich użytkowania. Przede wszystkim należy stosować odpowiednie środki ochrony osobistej, takie jak rękawice chemiczne, okulary ochronne oraz fartuchy laboratoryjne. Ważne jest również zapewnienie odpowiedniej wentylacji w pomieszczeniu, w którym znajduje się destylarka, aby uniknąć gromadzenia się szkodliwych oparów chemicznych. Użytkownicy powinni być świadomi właściwego postępowania w przypadku awarii lub wycieku substancji chemicznych – konieczne jest posiadanie planu działania oraz odpowiednich materiałów absorpcyjnych do neutralizacji ewentualnych zagrożeń. Regularne przeglądy techniczne urządzeń oraz ich konserwacja są kluczowe dla zapewnienia bezpieczeństwa pracy; należy zwracać szczególną uwagę na uszczelki i połączenia, które mogą ulegać zużyciu i prowadzić do wycieków.
Jakie innowacje technologiczne wpływają na rozwój destylarek
W ostatnich latach obserwuje się dynamiczny rozwój technologii związanych z produkcją destylarek do rozpuszczalników, co przekłada się na ich większą efektywność i wszechstronność zastosowań. Jednym z najważniejszych trendów jest automatyzacja procesów destylacyjnych; nowoczesne urządzenia często wyposażone są w zaawansowane systemy monitorujące oraz sterujące, które umożliwiają precyzyjne dostosowywanie parametrów pracy w czasie rzeczywistym. Dzięki temu możliwe jest osiągnięcie wyższej jakości produktów końcowych oraz zmniejszenie kosztów operacyjnych poprzez optymalizację zużycia energii i surowców. Innowacje obejmują także zastosowanie nowych materiałów konstrukcyjnych odpornych na działanie wysokich temperatur i agresywnych substancji chemicznych; dzięki temu urządzenia stają się bardziej trwałe i niezawodne. Ponadto rozwijane są technologie recyklingu rozpuszczalników organicznych, co przyczynia się do ochrony środowiska poprzez zmniejszenie ilości odpadów chemicznych generowanych podczas procesów przemysłowych.