
Budowa maszyn pneumatycznych opiera się na kilku kluczowych elementach, które współpracują ze sobą w celu efektywnego przetwarzania energii pneumatycznej. Podstawowym komponentem jest sprężarka, która odpowiada za wytwarzanie sprężonego powietrza. Sprężarki mogą mieć różne typy, takie jak tłokowe, śrubowe czy wirnikowe, a ich wybór zależy od specyfiki zastosowania. Kolejnym istotnym elementem są zbiorniki ciśnieniowe, które przechowują sprężone powietrze i zapewniają jego stabilny przepływ do pozostałych części systemu. W budowie maszyn pneumatycznych nie można zapomnieć o zaworach, które kontrolują kierunek i przepływ powietrza w układzie. Zawory te mogą być ręczne lub automatyczne, a ich odpowiedni dobór ma kluczowe znaczenie dla wydajności całego systemu. Również siłowniki pneumatyczne odgrywają ważną rolę, ponieważ przekształcają energię sprężonego powietrza na ruch mechaniczny.
Jakie są zalety i wady maszyn pneumatycznych
Maszyny pneumatyczne mają wiele zalet, które sprawiają, że są popularnym wyborem w różnych branżach przemysłowych. Przede wszystkim charakteryzują się dużą niezawodnością oraz prostotą obsługi. W porównaniu do innych systemów napędowych, takich jak hydraulika czy elektryka, maszyny pneumatyczne są mniej podatne na awarie związane z przegrzewaniem czy przeciążeniem. Dodatkowo ich konstrukcja jest zazwyczaj lżejsza i bardziej kompaktowa, co ułatwia integrację z innymi urządzeniami. Inną istotną zaletą jest możliwość szybkiej regulacji prędkości oraz siły działania siłowników pneumatycznych, co pozwala na precyzyjne dostosowanie parametrów pracy do wymagań konkretnej aplikacji. Mimo licznych zalet maszyny pneumatyczne mają również swoje wady. Jedną z nich jest konieczność dostarczania sprężonego powietrza z zewnętrznego źródła, co może generować dodatkowe koszty związane z eksploatacją sprężarek oraz utrzymaniem instalacji.
Jakie zastosowania mają maszyny pneumatyczne w przemyśle
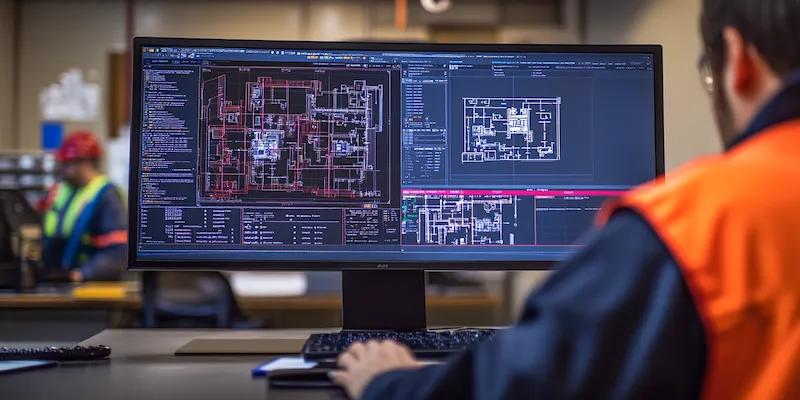
Maszyny pneumatyczne znajdują szerokie zastosowanie w różnych dziedzinach przemysłu ze względu na swoją wszechstronność i efektywność. W sektorze produkcyjnym są wykorzystywane do automatyzacji procesów montażowych oraz pakowania produktów. Siłowniki pneumatyczne mogą napędzać roboty przemysłowe, które wykonują precyzyjne operacje takie jak chwytanie, przenoszenie czy składanie elementów. W branży motoryzacyjnej maszyny pneumatyczne służą do malowania oraz lakierowania pojazdów dzięki swojej zdolności do równomiernego rozprowadzania farby pod ciśnieniem. W obszarze transportu pneumatycznego wykorzystuje się je do przesyłania materiałów sypkich lub granulowanych na krótkich i długich dystansach, co zwiększa efektywność procesów logistycznych. W przemyśle spożywczym maszyny pneumatyczne są wykorzystywane do napełniania opakowań oraz transportu produktów przez linie produkcyjne.
Jakie są nowoczesne technologie w budowie maszyn pneumatycznych
Nowoczesne technologie znacząco wpłynęły na rozwój budowy maszyn pneumatycznych, wprowadzając innowacyjne rozwiązania zwiększające ich wydajność oraz funkcjonalność. Jednym z najważniejszych trendów jest automatyzacja procesów sterowania maszynami pneumatycznymi za pomocą systemów PLC (Programmable Logic Controller), które umożliwiają precyzyjne zarządzanie pracą urządzeń oraz monitorowanie ich stanu w czasie rzeczywistym. Dzięki temu możliwe jest szybsze reagowanie na zmiany warunków pracy oraz optymalizacja procesów produkcyjnych. Kolejnym istotnym osiągnięciem technologicznym jest rozwój inteligentnych czujników ciśnienia i przepływu powietrza, które pozwalają na bieżące monitorowanie parametrów pracy maszyn i automatyczne dostosowywanie ich ustawień do aktualnych potrzeb produkcyjnych. Wprowadzenie technologii Internetu Rzeczy (IoT) umożliwia zdalne zarządzanie i diagnostykę systemów pneumatycznych, co zwiększa komfort użytkowania oraz minimalizuje ryzyko awarii.
Jakie są kluczowe zasady bezpieczeństwa w pracy z maszynami pneumatycznymi
Bezpieczeństwo w pracy z maszynami pneumatycznymi jest niezwykle istotne, ponieważ niewłaściwe użytkowanie tych urządzeń może prowadzić do poważnych wypadków. Kluczową zasadą jest zawsze przestrzeganie instrukcji obsługi dostarczonych przez producenta. Pracownicy powinni być odpowiednio przeszkoleni w zakresie obsługi maszyn pneumatycznych oraz znajomości ich budowy i funkcji. Ważnym aspektem jest również regularne przeprowadzanie przeglądów technicznych, które pozwalają na wykrycie ewentualnych usterek oraz zapobieganie awariom. Należy zwrócić szczególną uwagę na stan przewodów pneumatycznych, złączek oraz innych elementów układu, aby uniknąć wycieków sprężonego powietrza, które mogą prowadzić do niebezpiecznych sytuacji. Użytkownicy powinni także nosić odpowiednie środki ochrony osobistej, takie jak okulary ochronne czy rękawice, aby zminimalizować ryzyko urazów. Warto również pamiętać o stosowaniu osłon zabezpieczających wokół ruchomych części maszyn, co dodatkowo zwiększa poziom bezpieczeństwa w miejscu pracy.
Jakie są najczęstsze problemy związane z maszynami pneumatycznymi
Maszyny pneumatyczne, mimo swojej niezawodności, mogą napotykać różnorodne problemy, które wpływają na ich wydajność i funkcjonalność. Jednym z najczęstszych problemów jest spadek ciśnienia sprężonego powietrza, który może wynikać z nieszczelności w układzie lub niewłaściwego ustawienia sprężarki. Nieszczelności mogą występować w przewodach, złączach lub zaworach, co prowadzi do utraty efektywności całego systemu. Kolejnym powszechnym problemem są awarie siłowników pneumatycznych, które mogą być spowodowane zużyciem uszczelek lub innymi uszkodzeniami mechanicznymi. Takie awarie często objawiają się brakiem ruchu lub nieregularnym działaniem siłownika. Inne trudności mogą dotyczyć systemów sterowania, gdzie błędy w programowaniu lub awarie komponentów elektronicznych prowadzą do nieprawidłowego działania maszyny. Warto również zwrócić uwagę na problemy związane z kondensacją wilgoci w układzie pneumatycznym, co może prowadzić do korozji elementów oraz obniżenia jakości sprężonego powietrza.
Jakie są różnice między maszynami pneumatycznymi a hydraulicznymi
Maszyny pneumatyczne i hydrauliczne to dwa różne typy systemów napędowych, które mają swoje unikalne cechy oraz zastosowania. Podstawową różnicą między nimi jest medium robocze – maszyny pneumatyczne wykorzystują sprężone powietrze, podczas gdy hydrauliczne opierają się na cieczy hydraulicznej. Ta różnica ma wpływ na wiele aspektów ich działania. Maszyny pneumatyczne są zazwyczaj lżejsze i bardziej kompaktowe niż hydrauliczne, co czyni je bardziej mobilnymi i łatwiejszymi do integracji w różnych aplikacjach przemysłowych. Z drugiej strony systemy hydrauliczne charakteryzują się większą mocą i zdolnością do generowania wyższych momentów obrotowych, co sprawia, że są bardziej efektywne w zastosowaniach wymagających dużych sił. Kolejną istotną różnicą jest sposób regulacji prędkości i siły działania – w przypadku maszyn pneumatycznych można to osiągnąć poprzez regulację ciśnienia sprężonego powietrza, natomiast w hydraulice wykorzystuje się zawory kontrolujące przepływ cieczy.
Jakie są przyszłe kierunki rozwoju technologii maszyn pneumatycznych
Przyszłość technologii maszyn pneumatycznych wydaje się obiecująca dzięki ciągłemu postępowi technologicznemu oraz rosnącym wymaganiom przemysłu. Jednym z kluczowych kierunków rozwoju jest integracja maszyn pneumatycznych z nowoczesnymi systemami automatyki przemysłowej oraz sztucznej inteligencji. Dzięki temu możliwe będzie tworzenie bardziej zaawansowanych systemów sterowania, które będą potrafiły samodzielnie optymalizować procesy produkcyjne oraz dostosowywać parametry pracy do zmieniających się warunków rynkowych. Również rozwój technologii IoT (Internet of Things) umożliwi zdalne monitorowanie stanu maszyn oraz zbieranie danych dotyczących ich wydajności, co pozwoli na szybsze diagnozowanie problemów i podejmowanie działań prewencyjnych. Ponadto coraz większy nacisk kładzie się na efektywność energetyczną oraz ekologiczne aspekty produkcji sprężonego powietrza, co może prowadzić do rozwoju nowych technologii sprężarek o niższym zużyciu energii oraz mniejszym wpływie na środowisko naturalne.
Jakie są koszty eksploatacji maszyn pneumatycznych
Koszty eksploatacji maszyn pneumatycznych obejmują szereg czynników, które wpływają na całkowite wydatki związane z ich użytkowaniem. Pierwszym istotnym elementem są koszty energii związane z działaniem sprężarek powietrza. W zależności od wielkości zakładu oraz intensywności użytkowania sprężarek te koszty mogą być znaczne. Dlatego ważne jest optymalizowanie zużycia energii poprzez odpowiednie zarządzanie pracą urządzeń oraz ich konserwację. Kolejnym czynnikiem wpływającym na koszty eksploatacji są wydatki związane z konserwacją i serwisowaniem maszyn pneumatycznych. Regularne przeglądy techniczne oraz wymiana zużytych części są niezbędne dla zapewnienia niezawodności działania urządzeń i minimalizacji ryzyka awarii. Dodatkowo warto uwzględnić koszty materiałów eksploatacyjnych takich jak oleje czy filtry powietrza, które również mają wpływ na ogólne wydatki związane z utrzymaniem systemu w dobrym stanie technicznym.
Jakie są najważniejsze trendy w projektowaniu maszyn pneumatycznych
W projektowaniu maszyn pneumatycznych można zaobserwować kilka istotnych trendów, które mają na celu zwiększenie ich efektywności oraz funkcjonalności. Jednym z nich jest miniaturyzacja komponentów, co pozwala na tworzenie bardziej kompaktowych i lekkich urządzeń, które łatwiej integrować w ograniczone przestrzenie produkcyjne. Również rozwój technologii symulacji komputerowej umożliwia inżynierom dokładniejsze modelowanie i testowanie systemów pneumatycznych przed ich wdrożeniem, co przyczynia się do redukcji kosztów oraz czasu potrzebnego na wprowadzenie nowych rozwiązań. Wzrost znaczenia zrównoważonego rozwoju wpływa na projektowanie maszyn, które są bardziej energooszczędne oraz przyjazne dla środowiska. Wykorzystanie materiałów o wysokiej wytrzymałości oraz niskiej wadze staje się standardem, co przekłada się na dłuższą żywotność urządzeń.