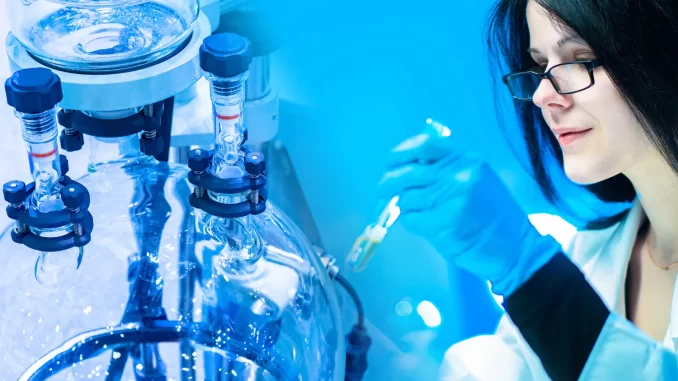
Destylator przemysłowy to urządzenie, które odgrywa kluczową rolę w procesach separacji substancji na różne składniki. Jego działanie opiera się na różnicy temperatur wrzenia poszczególnych komponentów mieszaniny. W praktyce, proces destylacji polega na podgrzewaniu cieczy do momentu, gdy zaczyna ona parować. Opary te następnie są schładzane i skraplane, co pozwala na uzyskanie czystych frakcji. W przemyśle chemicznym i petrochemicznym destylatory są wykorzystywane do oczyszczania surowców oraz produkcji różnych substancji chemicznych. W zależności od zastosowania, destylatory mogą mieć różne konstrukcje, takie jak kolumnowe czy prostokątne, a ich wydajność jest dostosowana do specyficznych potrzeb produkcyjnych. Warto również zauważyć, że nowoczesne destylatory często wyposażone są w zaawansowane systemy automatyzacji, co zwiększa ich efektywność oraz precyzję w procesie separacji.
Jakie są główne zastosowania destylatorów przemysłowych
Destylatory przemysłowe znajdują szerokie zastosowanie w różnych branżach, co czyni je niezwykle wszechstronnymi urządzeniami. Jednym z najważniejszych obszarów ich użycia jest przemysł chemiczny, gdzie służą do produkcji i oczyszczania substancji chemicznych, takich jak alkohole, kwasy czy rozpuszczalniki. W przemyśle petrochemicznym destylatory są kluczowe w procesie rafinacji ropy naftowej, umożliwiając wydobycie różnych frakcji paliwowych oraz olejów. Kolejnym istotnym zastosowaniem jest przemysł spożywczy, gdzie destylatory wykorzystywane są do produkcji napojów alkoholowych, takich jak whisky czy wódka, a także do ekstrakcji olejków eterycznych z roślin. W farmaceutyce destylacja odgrywa ważną rolę w oczyszczaniu substancji czynnych oraz ich izolacji.
Jakie są różnice między destylatorami przemysłowymi a laboratoryjnymi
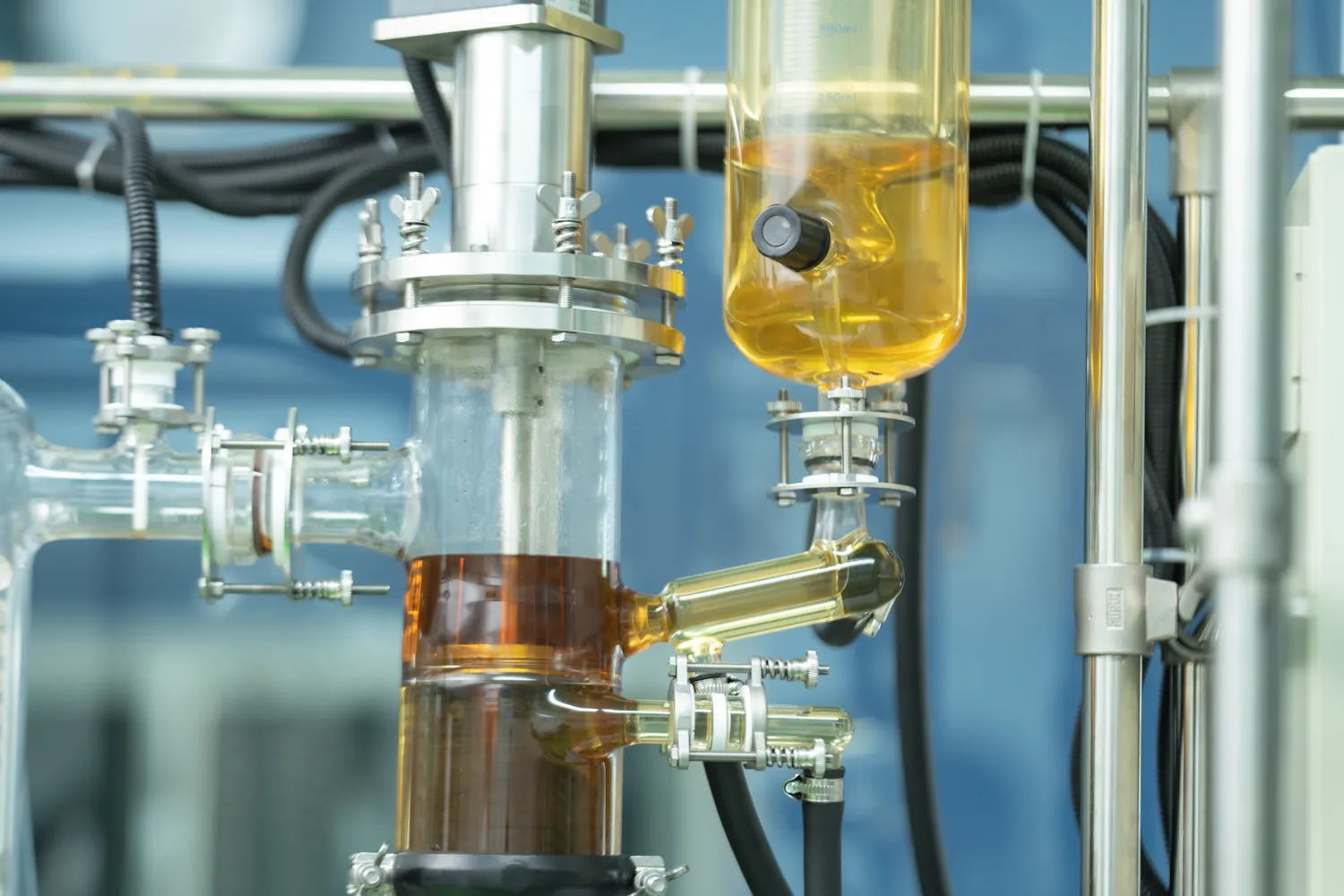
Destylatory przemysłowe i laboratoryjne różnią się przede wszystkim skalą produkcji oraz przeznaczeniem. Destylatory przemysłowe są zaprojektowane z myślą o dużych ilościach surowców i mają znacznie większą wydajność niż ich laboratoryjne odpowiedniki. W przemyśle często wymagane są urządzenia zdolne do pracy ciągłej przez długi czas, co wiąże się z koniecznością zastosowania bardziej zaawansowanych technologii oraz systemów automatyzacji. Z kolei destylatory laboratoryjne są zazwyczaj mniejsze i bardziej elastyczne, co umożliwia prowadzenie eksperymentów oraz testowanie różnych parametrów procesu destylacji. Różnice te obejmują także materiały użyte do budowy urządzeń; w laboratoriach często stosuje się szkło lub materiały odporne na korozję, podczas gdy w przemyśle dominują stal nierdzewna i inne trwałe materiały.
Jakie technologie wspierają nowoczesne destylatory przemysłowe
Nowoczesne destylatory przemysłowe korzystają z wielu innowacyjnych technologii, które zwiększają ich efektywność oraz precyzję działania. Jednym z kluczowych elementów jest automatyzacja procesów, która pozwala na monitorowanie i kontrolowanie parametrów pracy urządzenia w czasie rzeczywistym. Dzięki zastosowaniu czujników i systemów informatycznych możliwe jest optymalizowanie warunków pracy oraz minimalizacja strat surowców. Kolejną istotną technologią jest wykorzystanie zaawansowanych materiałów izolacyjnych i konstrukcyjnych, które poprawiają efektywność energetyczną destylatorów. Nowoczesne systemy chłodzenia oparte na wymiennikach ciepła również przyczyniają się do zwiększenia wydajności procesu skraplania oparów. Dodatkowo, rozwój technologii cyfrowych umożliwia integrację destylatorów z systemami zarządzania produkcją oraz analizą danych, co pozwala na lepsze planowanie i prognozowanie potrzeb produkcyjnych.
Jakie są kluczowe komponenty destylatora przemysłowego
Destylator przemysłowy składa się z kilku kluczowych komponentów, które współpracują ze sobą w celu efektywnego przeprowadzenia procesu destylacji. Podstawowym elementem jest zbiornik, w którym umieszczana jest mieszanina do destylacji. Zbiornik ten jest zazwyczaj podgrzewany, co pozwala na odparowanie substancji o niższej temperaturze wrzenia. Opary, które powstają w wyniku podgrzewania, kierowane są do kolumny destylacyjnej, gdzie zachodzi proces separacji. Kolumna ta zawiera różne elementy, takie jak talerze czy wypełnienia, które zwiększają powierzchnię kontaktu między oparami a cieczą, co sprzyja dalszej separacji składników. Po przejściu przez kolumnę opary trafiają do kondensatora, gdzie są schładzane i skraplane. Skroplona ciecz zbierana jest w zbiorniku odbiorczym. Dodatkowo, nowoczesne destylatory mogą być wyposażone w systemy monitorujące i kontrolujące parametry pracy, co pozwala na optymalizację procesu oraz zwiększenie jego efektywności.
Jakie są najczęstsze problemy związane z destylatorami przemysłowymi
Podczas eksploatacji destylatorów przemysłowych mogą wystąpić różnorodne problemy, które wpływają na efektywność i jakość procesu destylacji. Jednym z najczęstszych problemów jest zatykanie kolumny destylacyjnej, co może prowadzić do obniżenia wydajności oraz jakości uzyskiwanych frakcji. Zatykanie może być spowodowane osadzaniem się zanieczyszczeń lub produktów ubocznych na elementach kolumny. Innym powszechnym problemem jest niewłaściwe ustawienie parametrów pracy, takich jak temperatura czy ciśnienie, co może prowadzić do nieefektywnej separacji składników. W przypadku niewłaściwego chłodzenia oparów może również dojść do ich ponownego odparowania, co skutkuje stratami surowców. Dodatkowo, awarie systemów automatyzacji mogą prowadzić do niekontrolowanych zmian w procesie produkcyjnym. Regularne przeglądy i konserwacja urządzeń są kluczowe dla minimalizacji ryzyka wystąpienia tych problemów oraz zapewnienia ciągłości produkcji.
Jakie są koszty związane z użytkowaniem destylatorów przemysłowych
Koszty związane z użytkowaniem destylatorów przemysłowych obejmują wiele aspektów, które należy uwzględnić przy planowaniu inwestycji oraz eksploatacji tych urządzeń. Pierwszym i najważniejszym kosztem są wydatki na zakup samego urządzenia, które mogą się znacznie różnić w zależności od jego wielkości, rodzaju oraz zastosowania. Kolejnym istotnym elementem kosztowym są wydatki operacyjne związane z energią potrzebną do podgrzewania cieczy oraz chłodzenia oparów. Koszty te mogą być znaczące, zwłaszcza w przypadku dużych instalacji pracujących na pełnych obrotach przez długi czas. Dodatkowo należy uwzględnić koszty materiałów eksploatacyjnych oraz konserwacyjnych, które są niezbędne do utrzymania urządzenia w dobrym stanie technicznym. Warto także pamiętać o kosztach związanych z zatrudnieniem wykwalifikowanego personelu obsługującego destylatory oraz szkoleń dla pracowników.
Jakie są przyszłe trendy w technologii destylacji przemysłowej
Przemysłowa technologia destylacji stale się rozwija i ewoluuje w odpowiedzi na zmieniające się potrzeby rynku oraz rosnące wymagania dotyczące efektywności energetycznej i ochrony środowiska. Jednym z kluczowych trendów jest coraz większa automatyzacja procesów destylacyjnych, co pozwala na lepsze zarządzanie parametrami pracy oraz szybszą reakcję na zmiany warunków produkcyjnych. Nowoczesne systemy monitorujące umożliwiają zbieranie danych w czasie rzeczywistym i ich analizę, co sprzyja optymalizacji procesów oraz minimalizacji strat surowców. Kolejnym istotnym trendem jest rozwój technologii odzysku ciepła, która pozwala na wykorzystanie energii cieplnej generowanej podczas procesu destylacji do podgrzewania innych mediów lub procesów technologicznych. W kontekście ochrony środowiska rośnie także zainteresowanie ekologicznymi metodami separacji substancji chemicznych, które minimalizują negatywny wpływ na środowisko naturalne.
Jakie są wymagania dotyczące bezpieczeństwa dla destylatorów przemysłowych
Bezpieczeństwo pracy z destylatorami przemysłowymi jest kluczowym aspektem ich eksploatacji i wymaga przestrzegania rygorystycznych norm oraz standardów. Przede wszystkim każdy zakład musi posiadać odpowiednie procedury operacyjne dotyczące obsługi urządzeń oraz reagowania na sytuacje awaryjne. Wszyscy pracownicy powinni być odpowiednio przeszkoleni w zakresie bezpieczeństwa pracy oraz znajomości zasad działania destylatorów. Ważnym elementem jest także regularna konserwacja urządzeń oraz przeprowadzanie inspekcji technicznych mających na celu wykrycie ewentualnych usterek czy zagrożeń. Systemy zabezpieczeń powinny obejmować m.in. automatyczne wyłączniki awaryjne, czujniki ciśnienia i temperatury oraz systemy wentylacyjne zapobiegające gromadzeniu się niebezpiecznych oparów. Ponadto konieczne jest stosowanie odpowiednich materiałów budowlanych odpornych na działanie wysokich temperatur i ciśnienia.
Jakie są zalety korzystania z nowoczesnych destylatorów przemysłowych
Korzystanie z nowoczesnych destylatorów przemysłowych niesie ze sobą wiele korzyści zarówno dla producentów, jak i dla środowiska naturalnego. Przede wszystkim nowoczesne urządzenia charakteryzują się wyższą efektywnością energetyczną dzięki zastosowaniu innowacyjnych technologii odzysku ciepła oraz automatyzacji procesów produkcyjnych. To przekłada się na niższe koszty operacyjne oraz mniejsze zużycie surowców. Dodatkowo nowoczesne destylatory oferują większą precyzję separacji składników, co pozwala na uzyskanie wyższej jakości produktów końcowych oraz minimalizację strat materiałowych. Dzięki zaawansowanym systemom monitorującym możliwe jest szybkie dostosowywanie parametrów pracy do zmieniających się warunków produkcyjnych, co sprzyja elastyczności produkcji i lepszemu zarządzaniu zasobami.